Overview
Building Culture PLA is developing environmentally- and socially-responsible methods and components for timber construction. Our research is focused on ways to
- integrate irregular roundwood posts into conventional timber frame construction
- produce dimensional timbers without plain-sawing
- seamlessly join prefabricated panels.
Wood building products are commodities manufactured by capital- and energy-intensive, export-driven industries. Every step of a commodity manufacturing process aims to overcome the variation that characterizes its feedstock. The most effective way to homogenize a tree is to decompose it. Flaking, veneering, boiling, and crushing operations produce OSB, plywood, LVL, and other engineered wood products. Plain-sawing and finger-joining produces glulam, CLT, and dimensional timber. Glulam and CLT require petroleum-based binders. Each step of the decomposition/re-composition process demands energy and capital. Along the way, the macroscopic characteristics of a tree—the properties that make it a brilliant structural proposition—are destroyed.
We are researching different ways to manufacture timber building products: intermediate-technology solutions that are less capital- and energy-intensive than conventional industrial methods, but also less time- and skill-intensive than traditional methods.
Research goals
- Instead of destroying an important structural property of the tree—the presence of stronger fibers at the outer circumference of the trunk—we seek to take advantage of this property in the final structural element.
- We avoid plain-sawing. In this way we reduce stresses induced by differential radial and circumferential shrinkage. We work with wood’s desire to shrink and bend, not against it.
- We seek to increase the percent of the feedstock—a debarked tree—that is retained as solid wood in the final building product. In conventional processing operations, harvested trees are first turned into cylinders. We employ the tree trunk in the shape it naturally is: a truncated cone.
- We retain the maximum number of continuous fibers in the final building product and locate the strongest fibers where they are the most structurally effective.
- We don’t process the tree into perfect rectangular solids.
- We aim to produce timbers for rim beams and bearing plates, components in conventional timber frame construction. These elements should run continuously along each side of a building frame, so should be longer than conventional dimensional timbers (5.4 meters or 6.0 meters for finger-jointed timbers). They don’t need to resist large bending loads like glulam and LVL components, and should be less expensive.
Socially-responsible considerations
- Instead of producing building products in high-volume, energy- and capital-intensive plants that draw their feedstock from a large geographic area, produce them in local factories that draw upon regionally sourced timber.
- Instead of producing generic commodities, produce components suitable for special applications. For example, the elements we are developing are highly compatible with panelized prefabricated construction approaches.
- Introduce greater opportunity for SMEs in the building industry. Sweden has the most monopolized, energy-intensive, skill-intensive, and capital-intensive building industry in the world. In its Policy for the Designed Environment (prop. 2017/18:110), the Swedish government asked that “new and innovative material combinations and solutions be [developed and] promoted so that the use of sustainable materials can increase and that more sustainable buildings can be built… Increased industrial timber construction, based on sustainably produced forest raw materials, contributes to the development of a circular and bio-based economy and to new sustainable housing, and can create increased employment throughout the country.”
Accomplishments and milestones
- We built and equipped a 225 m2 prototyping facility in Södermanland County, Sweden, within a managed forest, that has the capacity to machine beams and posts up to 7 meters long. The facility is located in a renovated 19th Century barn.
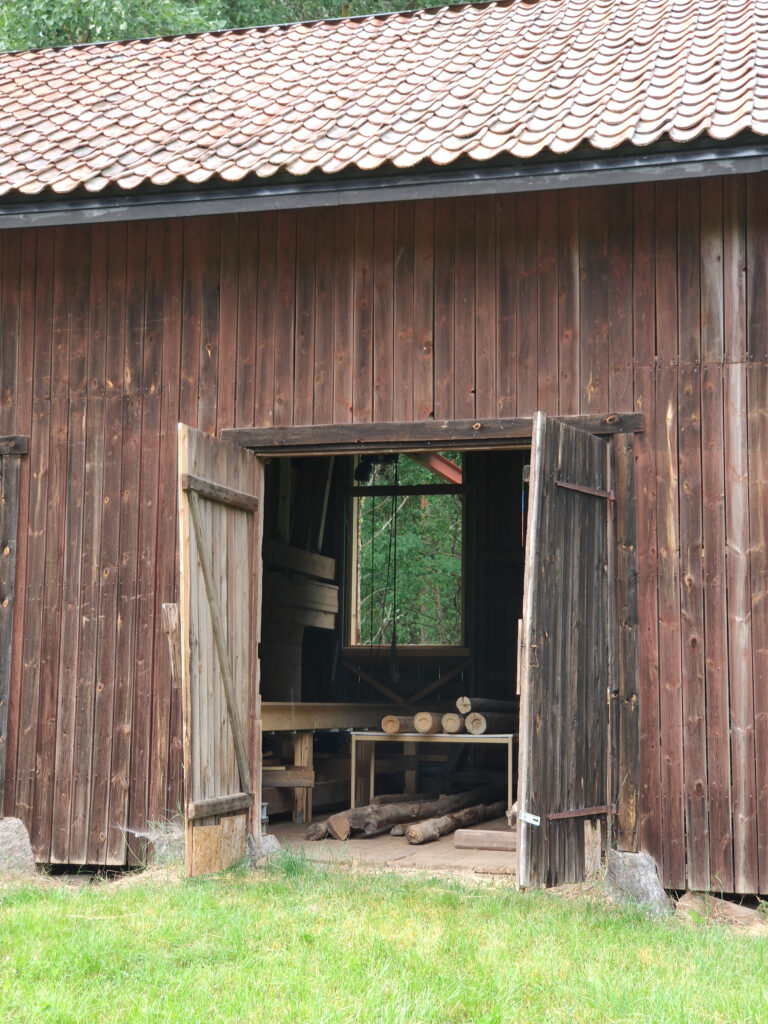
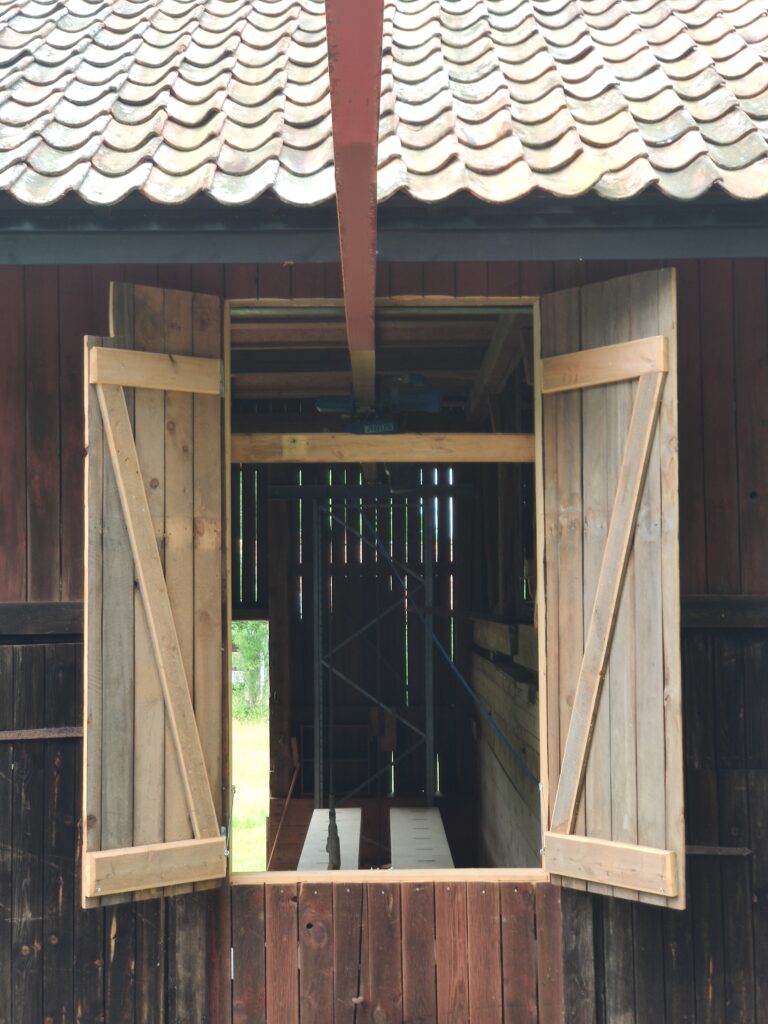
- We have developed and refined the manufacturing process for machining roundwood posts. Using special equipment, we cut a pair of V-shaped grooves along the length of the posts.
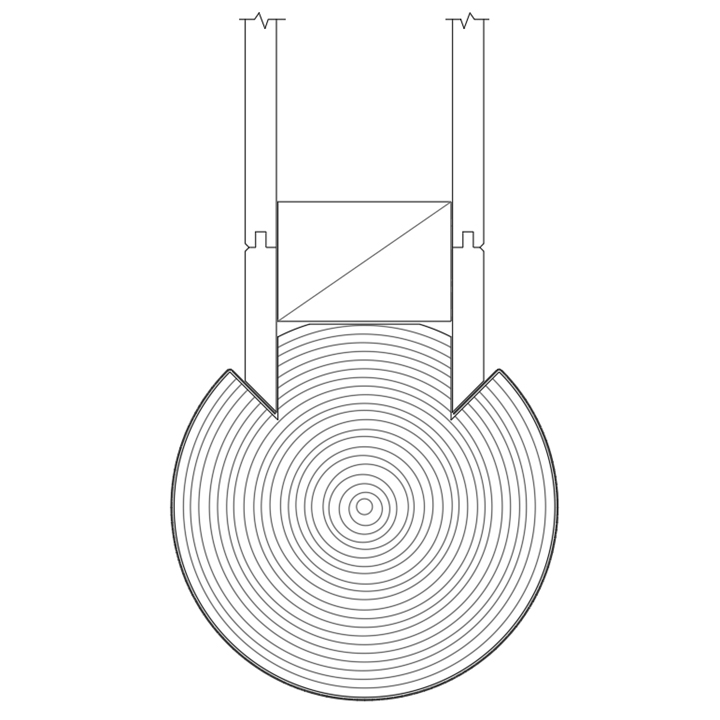
- The V-grooves receive the ends of wall panels, which slide into place and are fastened with blind connectors.
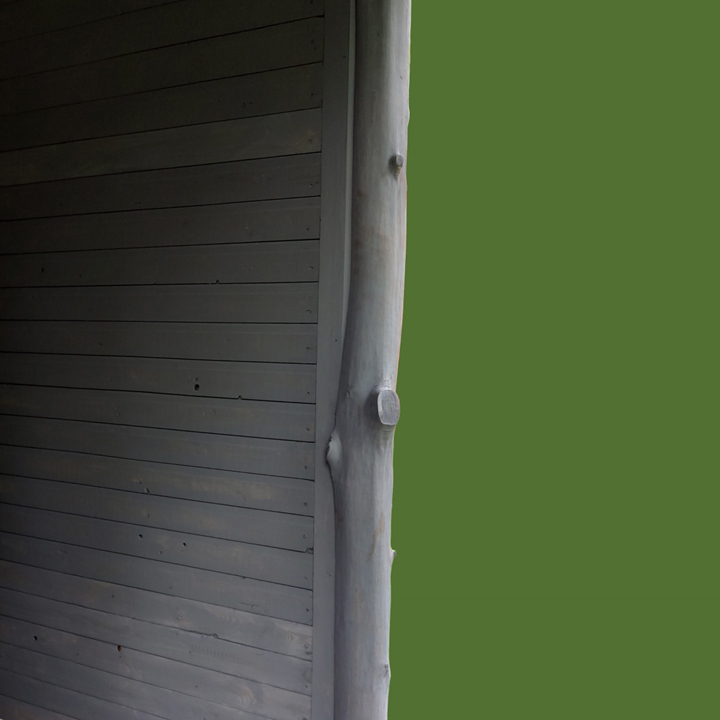
- The result is reminiscent of details in traditional Japanese architecture—for example the “daimebashira” post in a tokonoma niche, part of every traditional tea house. This roundwood post, which is chosen and prized for its irregular shape, receives the end of a plastered wing wall. The joint between post and wing wall requires masterful chisel work. We achieve similarly refined results with a less skill-intensive, less expensive “mechanized handicraft” approach.
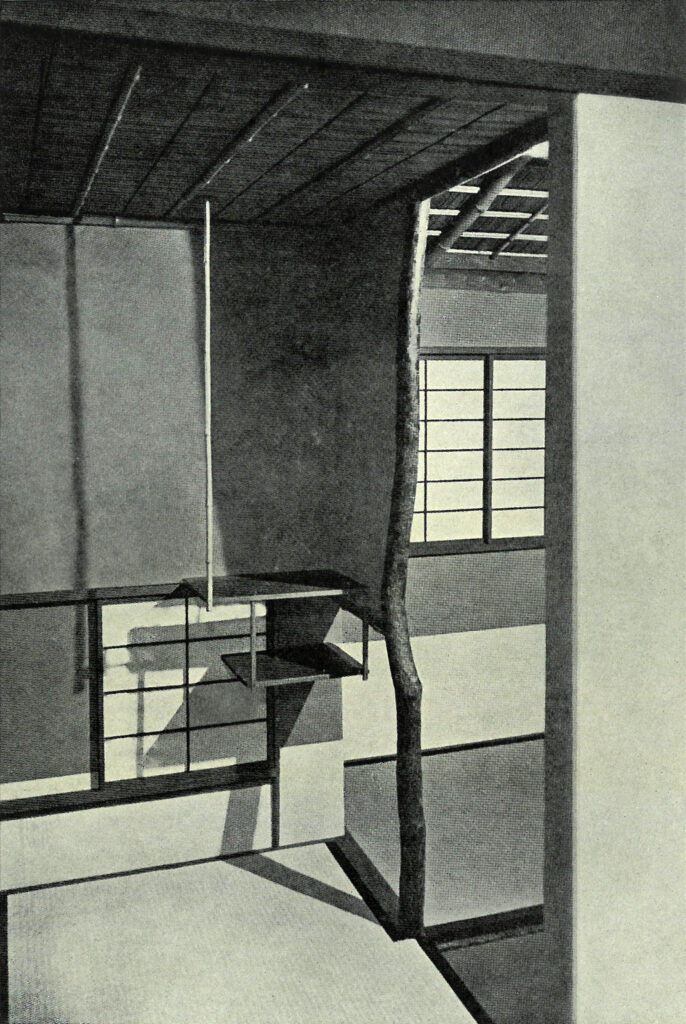
- Japanese carpenters set timbers on trestles in their woodshop and use special layout techniques to ensure that timbers are marked accurately before sawing and chiseling, so that the resulting structure is square and rigid. Instead of performing the layout and cutting in this traditional way, we set steel pins into the ends of the posts and place them within a special jig table. Each pin is supported on an adjustable jack. Once the post is correctly positioned, we screw a guide fence onto the jig table and use a large circular saw to cut the longitudinal V-shaped rabbets into the posts. The table provides a square frame of reference for the cutting process. Even though the posts are irregular, the rabbets are straight and plumb.
- We have machined posts of different species and diameters and tested them in a range of applications—most recently as corner posts for a pavilion at the Timescape Garden, Norrköping. For more info about the roundwood building system, contact Peter Lynch. Be sure to include “roundwood construction” in the subject headline.
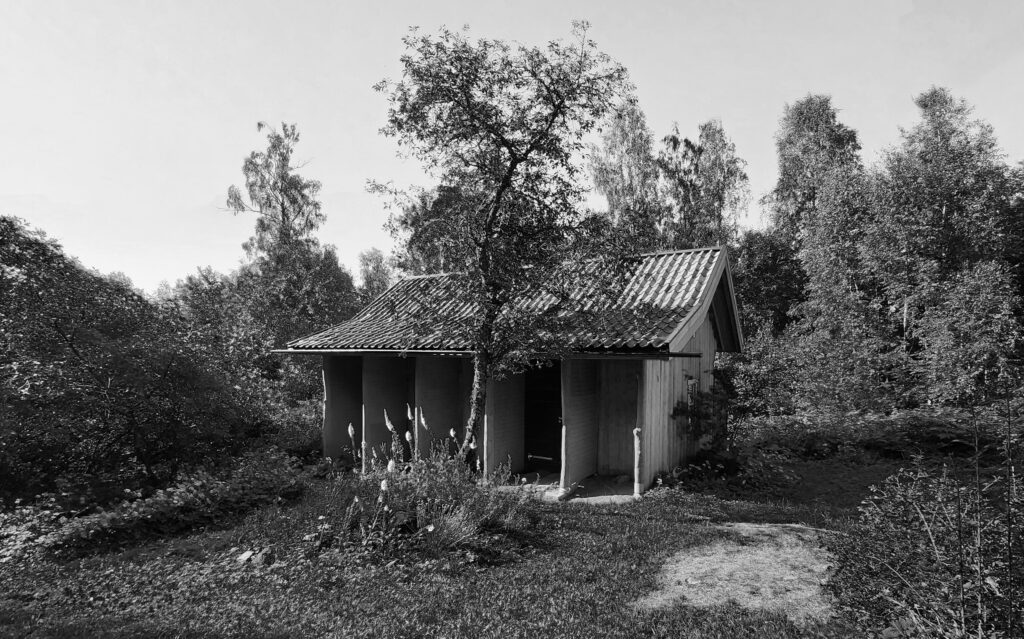
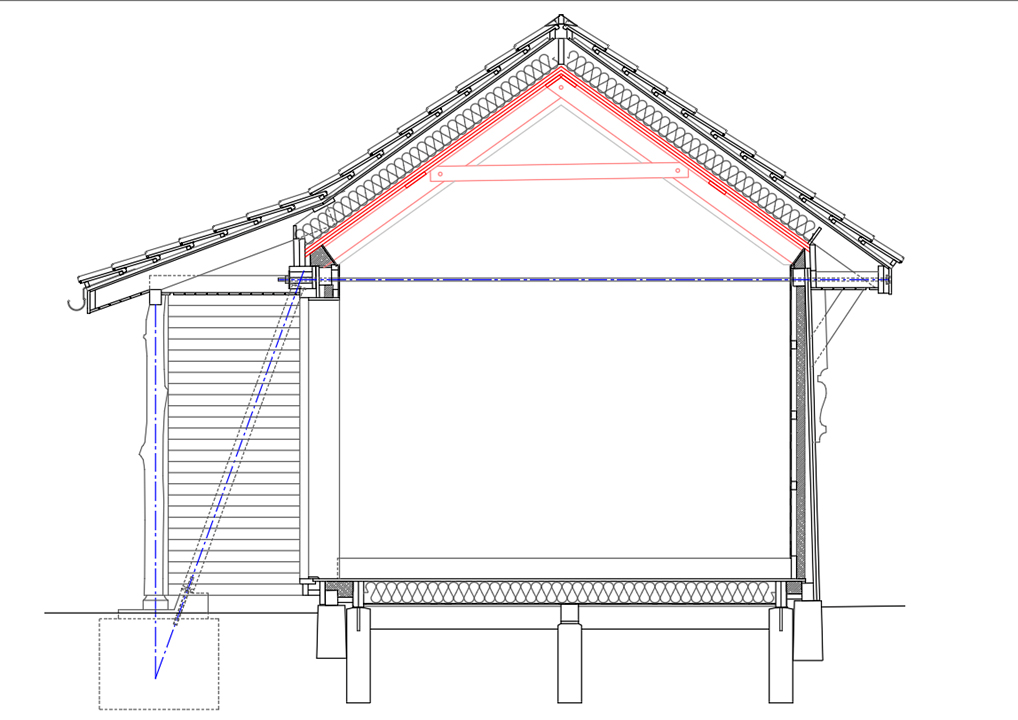
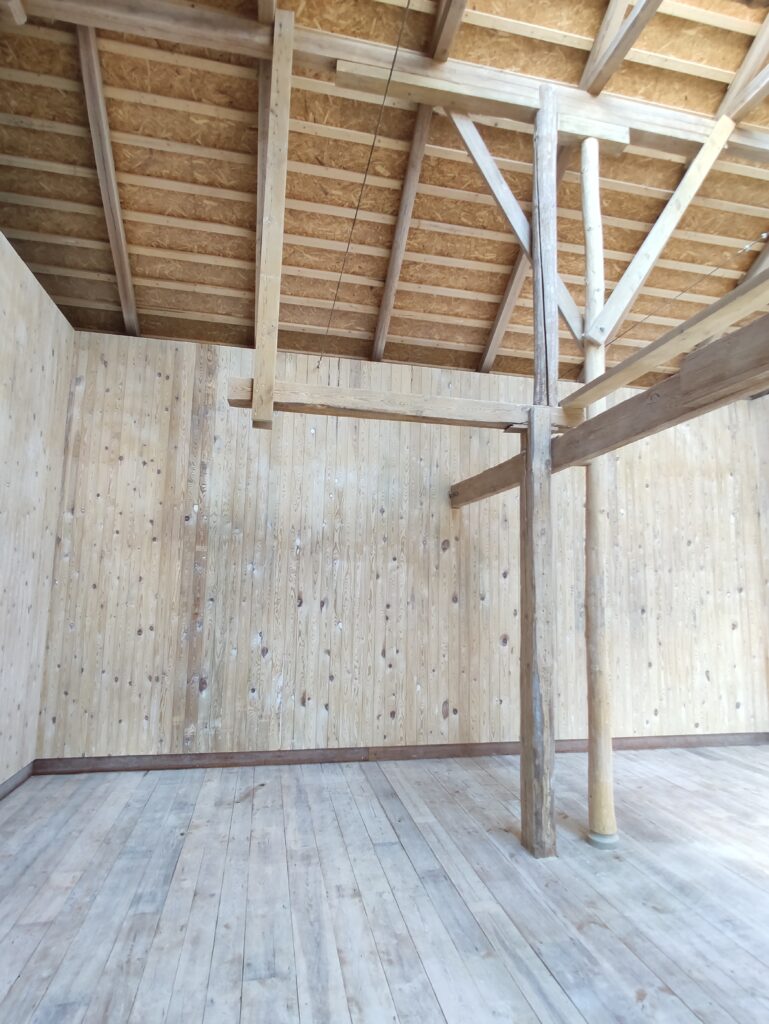